Why Quality Management Deserves More Attention
Every Malaysian business strives for efficiency, customer satisfaction, and long-term success. But behind the scenes, one crucial factor often determines whether a company thrives or struggles—quality management. Without effective quality management, companies face costly errors, damaging reputations, and loss of competitiveness. ISO 9001 certification helps businesses in Malaysia overcome these challenges by providing structured, proven solutions.
Many companies assume their current processes are “good enough,” but is that really the case? In this article, we’ll uncover the hidden challenges of poor quality management and why businesses need to take a closer look at their approach before it’s too late.
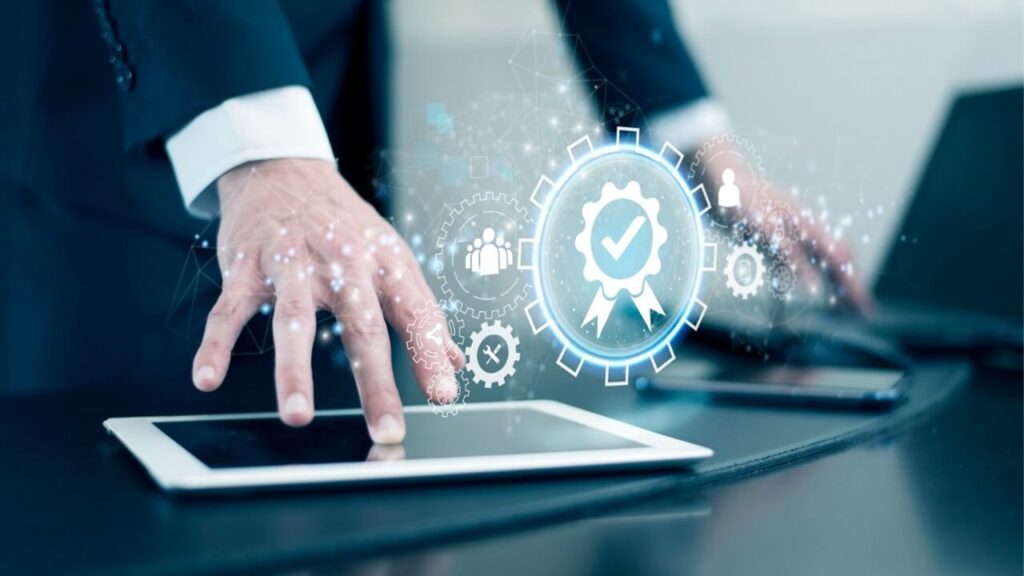
Why Quality Management Deserves More Attention
Every Malaysian business strives for efficiency, customer satisfaction, and long-term success. But behind the scenes, one crucial factor often determines whether a company thrives or struggles—quality management. Without effective quality management, companies face costly errors, damaging reputations, and loss of competitiveness. ISO 9001 certification helps businesses in Malaysia overcome these challenges by providing structured, proven solutions.
Many companies assume their current processes are “good enough,” but is that really the case? In this article, we’ll uncover the hidden challenges of poor quality management and why businesses need to take a closer look at their approach before it’s too late.
The Hidden Costs of Poor Quality Management
Quality isn’t just about delivering a good product, it’s about protecting your bottom line. Poor quality management can have severe consequences, both financially and reputationally. While many Malaysian businesses focus on upfront savings, the hidden costs of poor quality can far outweigh the initial investment in quality assurance.
Direct Financial Losses
Poor quality management leads to costly defects, rework, and customer complaints, resulting in substantial financial losses:
- Product Recalls & Rework Costs: Manufacturing defects don’t just affect one product, they lead to expensive recalls, wasted materials, and additional labor costs.
- Operational Inefficiencies: Poor processes slow down production, waste resources, and increase overhead costs, all of which hurt profitability.
- Customer Refunds & Warranty Claims: Each defective product sold means more refunds, repairs, and warranty claims—draining revenue and impacting customer satisfaction.
Indirect Financial Losses
Poor quality not only increases direct costs but also leads to long-term problems that slowly reduce profits and harm business sustainability:
- Brand Damage & Loss of Customer Loyalty: Quality issues lead to negative reviews and loss of trust. Once a brand’s reputation takes a hit, winning back customers isn’t easy.
- Legal & Compliance Issues: Regulatory fines, lawsuits, and product bans can be costly and damaging to business operations.
- Employee Morale & Productivity: Constantly fixing quality issues frustrates employees, lowers productivity, and increases turnover.
Real-World Quality Management Failures Case Studies
Poor quality management can lead to serious financial losses, legal consequences, and reputational damage. Below are real-world case studies from different industries, showcasing the impact of quality failures:
Automotive Industry
Defective parts and safety failures have led to massive recalls, legal actions, and loss of consumer trust. For instance, airbag malfunctions in major car brands have resulted in billions of dollars in settlements.
Hospitality Industry
Inconsistent service quality, hygiene issues, and customer dissatisfaction have caused hotels and restaurants to lose business and receive damaging online reviews. Poor training and lack of quality control can significantly impact guest experience.
Food & Beverage (F&B) Industry
Contamination, poor food handling, and non-compliance with regulations have caused food poisoning outbreaks, costly lawsuits, and brand boycotts. Several well-known chains have suffered public backlash due to quality failures.
Medical & Healthcare Industry
Faulty medical devices, misdiagnoses, and errors in patient care have led to severe health consequences, regulatory fines, and lawsuits. Inadequate quality control in this sector can be life-threatening.
4 Effective Ways Malaysian Businesses Can Prevent Quality Failures
Ensuring consistent quality is vital for Malaysian businesses to maintain customer satisfaction and operational efficiency. Implementing the following strategies can help prevent quality failures:
Regular Inspections & Testing
Detecting defects early helps prevent costly rework and customer complaints. Inspections should be carried out at different stages—before production, during manufacturing, and before delivery. Using automated quality control tools can further improve accuracy and efficiency.
Employee Training & Awareness
Employees are the first line of defense against quality issues. Regular training on best practices, company quality standards, and problem-solving skills ensures they can identify and address issues proactively. A workplace culture that values quality encourages accountability at every level.
Supplier & Vendor Quality Control
The quality of raw materials and components directly impacts the final product. Businesses must work with trusted suppliers, set clear quality expectations, and conduct regular audits to ensure standards are met. Establishing quality agreements helps hold suppliers accountable.
Establishing a Strong Internal Quality Framework
Businesses should develop structured quality management practices that align with operational goals. This includes setting clear quality objectives, standardizing internal processes, monitoring performance through data-driven tools, and fostering a culture of continuous improvement.
Implementing ISO 9001 Quality Management System in Malaysia
ISO 9001 is a globally recognized quality management system (QMS) that helps businesses streamline operations, reduce defects, and enhance customer satisfaction. It provides a structured framework for process standardization, risk management, and continuous improvement, ensuring consistent product and service quality.
By adopting ISO 9001, businesses in Malaysia can lower operational costs, improve regulatory compliance, and strengthen customer trust. The certification process involves defining quality objectives, training employees, conducting internal audits, and passing a final certification audit to demonstrate compliance. Implementing ISO 9001 not only improves efficiency but also positions companies for long-term growth and competitiveness.
Building a Stronger Business with an Integrated Management System (IMS)
Achieving ISO 9001 is just the beginning. Businesses can further strengthen operations by integrating multiple management systems into a single, cohesive framework. This approach improves efficiency, enhances compliance, and simplifies internal processes.
An Integrated Management System (IMS) combines ISO 9001 with other internationally recognized standards, such as:
- ISO 14001 – Establishes an effective environmental management system, helping businesses reduce their environmental impact and comply with regulatory requirements.
- ISO 45001 – Focuses on occupational health and safety, ensuring a safer work environment by identifying and mitigating workplace hazards.
- ISO 27001 – Strengthens information security by providing a structured approach to protecting sensitive data, minimizing cybersecurity risks, and ensuring compliance with data protection regulations.
- ISO 22000 – Enhances food safety management by setting strict guidelines for food production, handling, and distribution to prevent contamination and ensure consumer safety.
Protect Your Business from Costly Quality Failures
Investing in quality control and internationally recognized standards like ISO 9001 is key to building a resilient and efficient business. A well-structured quality management system helps prevent costly failures, enhances customer satisfaction, and ensures long-term success.
Is your business ready to strengthen its quality management practices? Now is the time to assess your current processes and take proactive steps toward ISO 9001 certification.